Controlling Pressure in UHV and Cryogenics
Reliability spurs innovation
Vacuum technologies have advanced the field of cryogenics, allowing researchers to push the frontiers of what we know and businesses to apply that knowledge and drive innovation across a wide range of industries. The intersection of vacuum and cryogenic sciences is a demanding one.
Pressure and temperature requirements create a playing field where only certain materials of construction and precise techniques and processes can play. Whether a component within a closed cryogenic system or a transfer link to be reused and repurposed, metal hoses are well suited for these exacting environments.
Design considerations for pulling vacuum
Pressure requirements are among the main reasons users opt for metal hoses, whether to accommodate high pressures or the lack thereof. And while many materials would buckle when pulling a vacuum, metal will not.
Tensile strengths of the commonly used 300 series austenitic stainless steels along with hose geometry, ensure these components maintain their shape under great hoop stress. Itโs important to remember that both ends of the hose need to be properly anchored. Otherwise, it will shrink once in operation.
There are additional considerations when working with vacuum jacketed hoses where the pressure differential may be greater than what we are used to. The pressure of the inner hose should always be greater than the pressure of the outer hose, as negative pressure on the inner hose could cause buckling. We would also need to ensure that, under pressure, the inner and outer hoses elongate to bring both braids into tension, thereby allowing the hose to reach its full pressure-carrying capacity. This will not happen if there is net external pressure on the inner hose.
Low-temperature properties
Many metals have good โroom temperatureโ characteristics, but they do not necessarily maintain those characteristics as temperatures decrease. Witness the way materials become brittle and break at low temperatures.
The 300 series stainless steels are suitable for low-temperature service and are thus classified as โcryogenic steels.โ Yield and tensile strengths actually improve for these materials as the temperature drops. While 304 and 316 have minimum design temperatures of -452 ยฐF, 321 has a minimum design temperature of -325 ยฐF and is limited to liquid nitrogen applications.
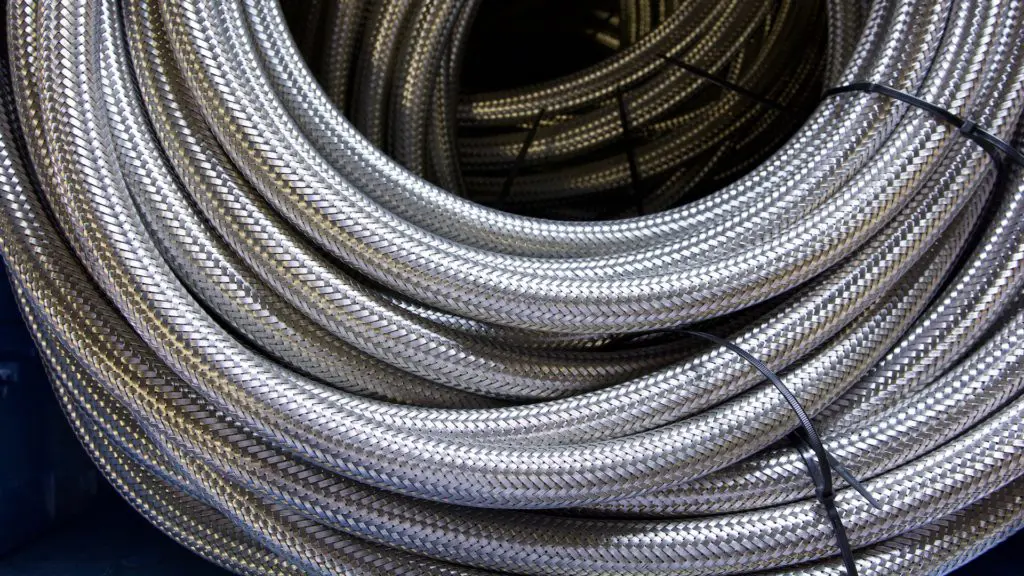
Dependability for UHV and cryogenics
With such a wide array of constructions, hoses remain a reliable means of fluid and gas conveyance that enable further creativity and ingenuity among original equipment manufacturers in this exciting space. Penflex has consistently refined its design, manufacturing and leak testing processes to best serve UHV and cryogenics markets.
Our annular, thin wall, compressed pitch cryogenic hoses prioritize flexibility and movement. Annular hoses, where individual corrugations are โstackedโ parallel to one another, consistently achieve longer dynamic cycling than helical hoses, where the corrugations are one continuous helix, given that bending happens between the corrugations rather than through them.
Made from thinner strip material, a thin wall hose requires less force to bend. This is a key indicator of flexibility, and an aim that is achieved further through placing the corrugations closer together and raising the height of them. A hose must be designed properly for the space it is to operate in, but with less risk of overbending and frictional damage due to sharp bends; a more flexible hose will generally be easier to install.
The utmost care is taken to prevent matter from settling within hoses during manufacturing and to produce hoses to the highest level of cleanliness. Our welders are certified to American Society of Mechanical Engineers Section IX, the industryโs highest standard. Welds are purged using argon gas, a proven process that enhances weld quality by decreasingโor even preventingโoxidation. This, in turn, maintains the corrosion resistance of parent materials and delivers contaminant free welds.
Once hoses pass visual inspection, a borescope is used to identify and remove any contaminants that may have entered the hose as a final step before leak testing. A mass spectrometer with helium tracer gas, one of the most accurate methods of leak detection, is then used to test the hoses. With the ability to detect leaks as small as 10-12 cubic centimeters per second, mass spectrometer testing reduces the risk of cryogen loss. The clean, controlled environments vacuums create to enable cryogenic processes depend upon reliable components such as these, which are similarly clean and leak tight.
This article on components for UHV and cryogenics originally ran in Cold Facts, The Magazine of the Cryogenic Society of America, Inc. Volume 38, Number 3, 2022.
About Penflex
Founded in 1902, Penflex is an ISO 9001-certified manufacturer of flexible metal piping solutions, offering a broad range of metal hose, braid, bellows and expansion joint products along with complementary services, including sales and welder training, engineering support, prototyping, testing and contract braiding. Known for quality and durability, our products are sold into multiple, unsynchronized vertical markets all over the world. Based in Gilbertsville, PA, Penflex maintains a warehouse in Houston, TX and operates a second manufacturing facility in Ho Chi Minh City, Vietnam.
More Articles
New Clean ID hose Streamlines the semiconductor supply chain
February 11, 2025
Penflex Receives CRN Approval for Metal Hose Assemblies Used in Turnaround Projects
October 29, 2024
Technology Advances Yield Clean ID Hose
May 29, 2024