Engineering Bulletin #156
Vibration is common in many piping systems. However, once it becomes a defining characteristic of the application it is safe to assume that vibration poses some very real risks to system integrity.
Deciding whether an application is โhigh vibrationโ is mostly a matter of opinion. Ascertaining amplitude without the use of sophisticated measuring equipment is difficult. Even if vibration could be quantified, design codes offer little in the way of defined limits.
Indications of Vibration Induced Failure
Circumferential cracks, typically on the crest but also in the valley of the corrugation, are symptomatic of vibration fatigue.
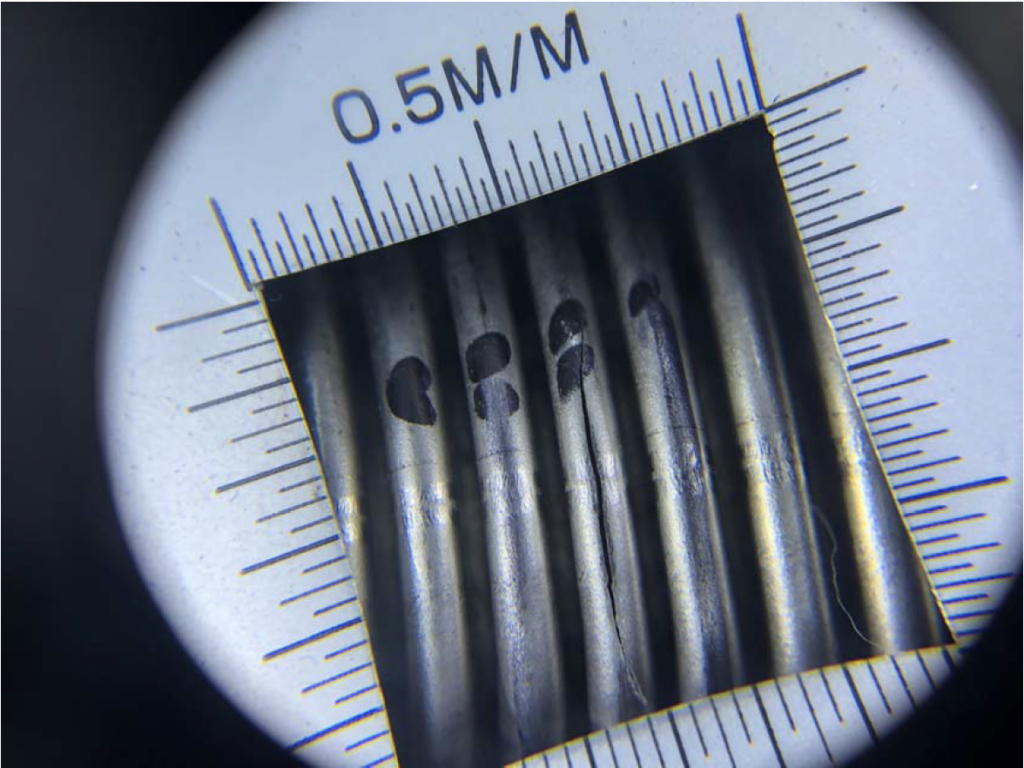
So too is braid wear. Braid wear is indicative of significant movement of the braid relative to the hose, like what you might expect to see in high vibration applications. The tensile strength of the braid wires is higher than that of the hose, so the hose loses material first.
In essence, the braid wires โsawโ into the hose, creating divots as seen below.
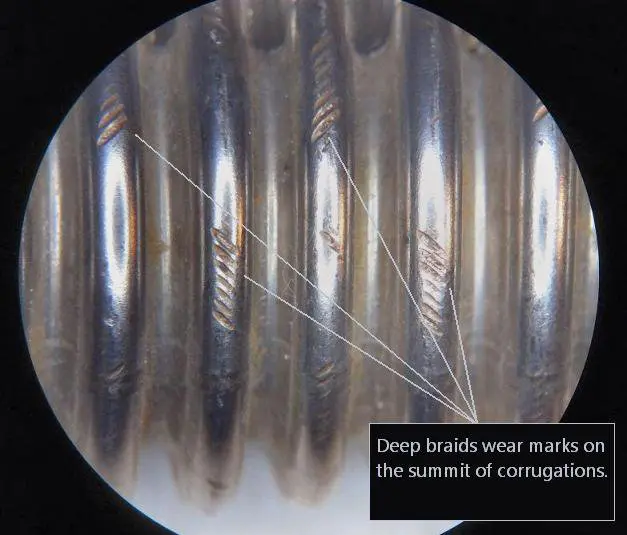
It’s important to note these indicators are not exclusive to vibration fatigue. Cracks can be a sign of torsion while braid wear can also result from mishandling. However, if a hose has failed due to vibration, it is likely that cracks or braid wear will be visible upon inspection.
Causes of Excessive Vibration in Piping Systems
Mechanical vibrations from pumps or moving equipment attached to the hose can induce movements that create premature ware and early failures.
Another kind of vibration is โflow induced,โ generally caused by high flow velocity inside the hose. The rule of thumb for maximum recommended flow velocity in a straight run of braided hose is 150 ft/sec for gas and 75 ft/sec for liquids.
Considerations for High Vibration Applications
There are no hard-and-fast rules when it comes to vibration. As a result, one can only attack the problem through trial and error.
When vibration failures occur, the typical response is to change the mass or stiffness of the assembly. Sometimes a combination of the two will yield a better result. Adding components such as external bend restrictors, additional braids and internal flow liners or increasing wall thickness can all be inexpensive fixes to overcome premature vibration failures.
Flexibility is another important consideration in high vibration applications, and there are some requirements as to minimum live length of a hose assembly in such scenarios. Those requirements can be found in this table here.
In the video below, Penflex Director of Quality and Engineering Janet Ellison discusses how to approach installing hoses in high vibration applications.