Engineering Bulletin #171
You’ve fallen and banged up your arm quite badly. There are scrapes and bruises and you’re in a lot of pain. You worry something might really be wrong and so you go to the emergency room for an x-ray. The radiograph confirms what the naked eye cannot: a broken bone.
X-ray technology can be used to see the inside of a weld as well as the inside of your arm. When electromagnetic waves pass through a material, the image rendered will reveal any imperfections. For instance, the digital reading shown here from an radiographic testing inspection on a butt weld shows slight darkness within the weld. This is an indication of incomplete fusion.
Welds that pass radiographic testing inspection will show complete fusion and be absent of any porosity.
The Most Sensitive NDT Inspection Methods
Any discussion of non-destructive testing (NDT) for metal hoses would be remiss if it failed to acknowledge the limited scope of methods used.
There are numerous NDT methods, some of which contain multiple techniques for reaching similar conclusions though with varying levels of granularity given the use of different equipment and the adherence to different processes.
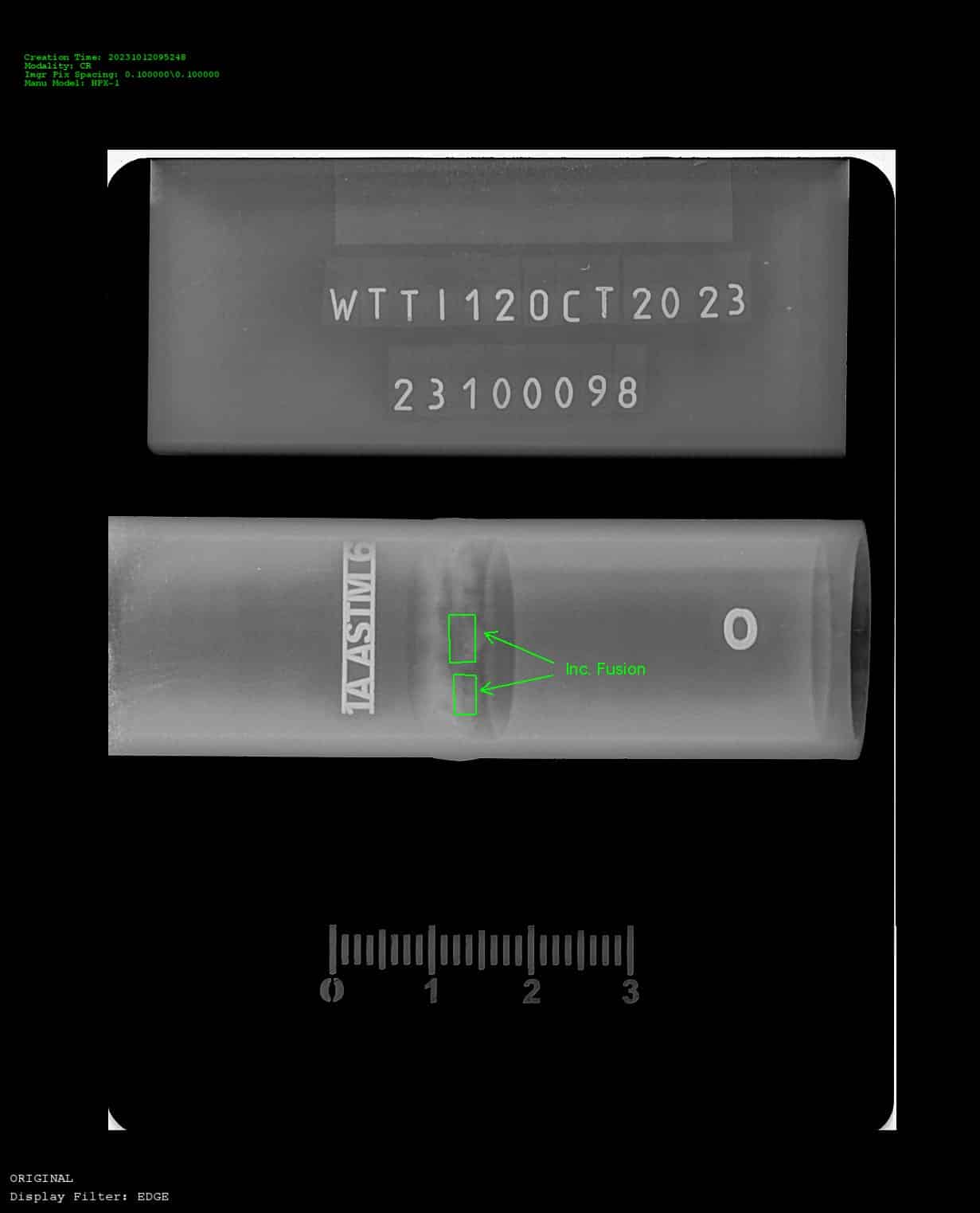
Leak testing (LT) is the most common NDT method for metal hoses. All Penflex hoses undergo LT inspection of seam and orbital welds. If being made into assemblies, the hoses are then subjected to air under water and hydrostatic tests to assess end fitting connections. For certain applications, we can use a helium mass spectrometer to identify even smaller leaks. While these techniques allow us to identify current leaks, they offer no indication of whether future leaks may occur.
For this, we may perform penetrant inspection (PT) on the hose. PT highlights surface defects like pits or cracks that could develop into leaks once the hose is in operation.
And, while Radiographic Testing is most often used on full penetration butt welds on pipe, tank and plate joints, if requested, we can support Radiographic Testing of hoses–whether that be to inspect the longitudinal seam or the end fitting connection welds. Radiographic testing is included within a subset of NDT inspection called volumetric testing, which entails looking at the whole mass from top to bottom. These are the most sensitive NDT methods.
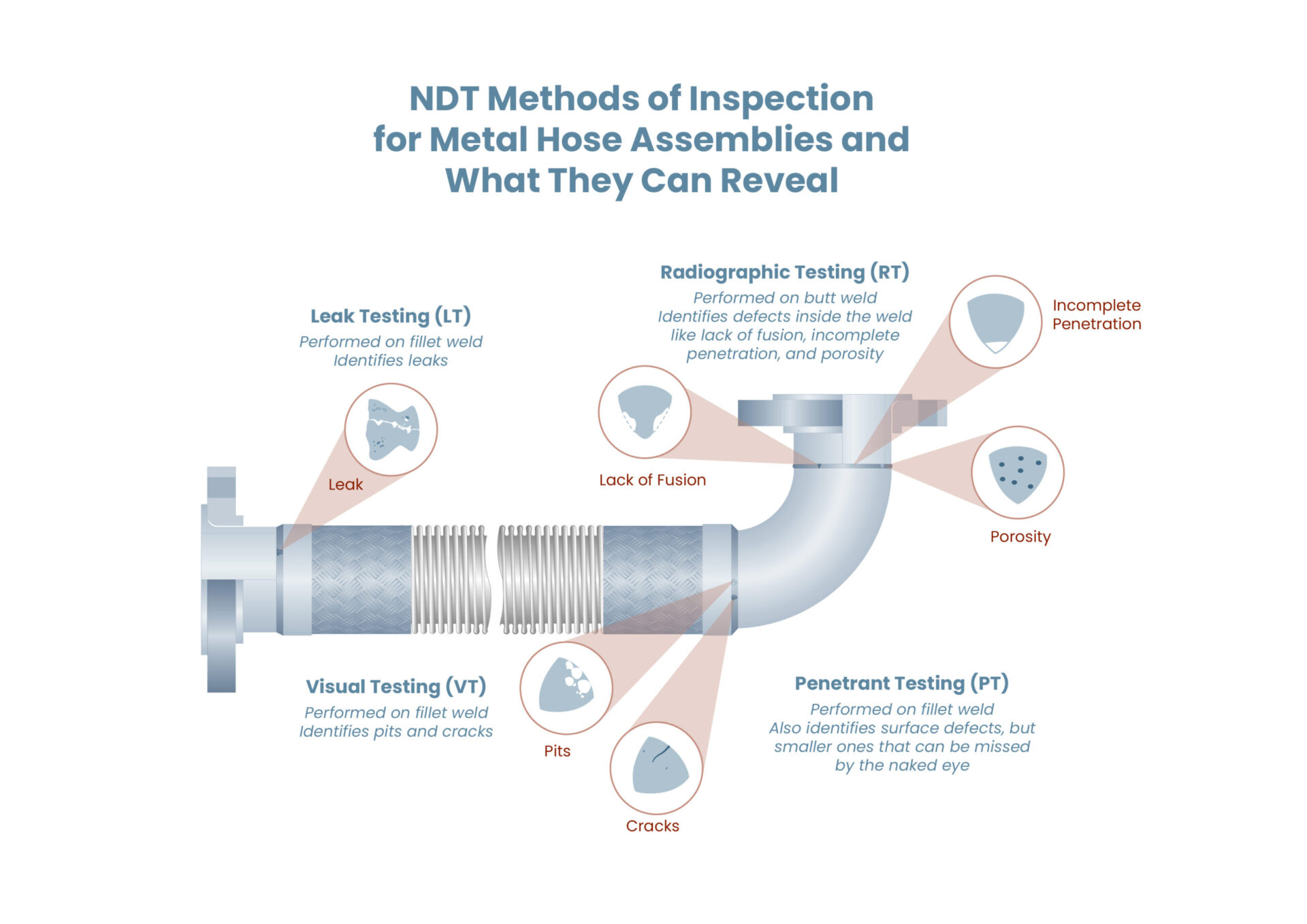
Governed by ASME
Radiographic testing is typically a request in scenarios where failure presents serious risks to safety. These could be applications in aerospace or nuclear power plants, for example. Radiographic testing gives piping system owners and equipment manufacturers greater assurance that components will perform as expected in the intended application. In other applications, such assurances may be unnecessary.
While RT does provide an additional means of measuring quality, it is also a requirement for compliance with ASME B31.3, the organization’s standard for process piping systems. If a plant is ASME B31.3 compliant, its pipe and hoses must be compliant with the code as well. Radiographic testing is among the requirements for compliance.
All NDT examination methods are outlined in Section V of the ASME Boiler and Pressure Vessel Code. Radiographic testing requirements, methods and techniques are detailed in Article 2 of the 1000-page-plus document.
Radiographic Testing in Combination with Other NDT Inspection Methods
ASME B31.3 often requires radiographic testing inspection in combination with another NDT method, typically visual inspection (VT). If a component fails VT, it would not then be subjected to radiographic testing. Beyond avoiding unnecessary testing, combining methods provides a more comprehensive view of the finished assembly in all aspects of surface conditions and weld quality.
The requirements for testing depend on fluid service. For instance, Category D Fluid Service covers non-flammable and non-toxic media flowing through the hose at temperatures ranging from -20°F to – 366°F at a maximum pressure of 150 PSI. Hoses used in this fluid service must undergo air under water and hydrostatic tests, as well as VT inspection, and 5% of each welder’s work is subjected to radiographic testing.
Then consider the requirements for Category M Fluid Service which governs highly toxic media flow. Air under water and hydrostatic tests are followed by VT and finally radiographic testing on 20% of all butt and miter joints.
Challenges of Radiographic Testing of Welds
The most obvious challenges to radiographic testing inspection include the equipment requirements, administration of inspection by qualified personnel, and the necessity of carrying out testing far from personnel or in a protected space where radiation can be contained.
The inspector needs a good set-up to take the right views and must be well versed in what they are looking at. While the code focuses on radiographic testing inspection of butt welds, radiographic testing can be carried out on any type of weld. This may present a challenge for metal hosers as some labs may never have seen the cap weld to fillet weld connections that are so ubiquitous in our industry.
For a successful inspection, the tester must understand the “load path” from end fitting to hose into braid.
NDT Radiographic Testing Requirements for a Weld Shop
Beyond satisfying user requirements, radiographic testing inspection is used to demonstrate a welder’s capability. As a shop that does work per ASME B31.3, Penflex must test at least 5% of all butt welds performed by each welder on a routine basis whether the work itself has a B31.3 requirement or not.
A welder who consistently passes radiographic testing inspection is a very skilled welder indeed.
This butt weld connecting a 304 stub end to a concentric reducer is an example of a high quality weld. Something like this would be used as part of the 5% requirement.
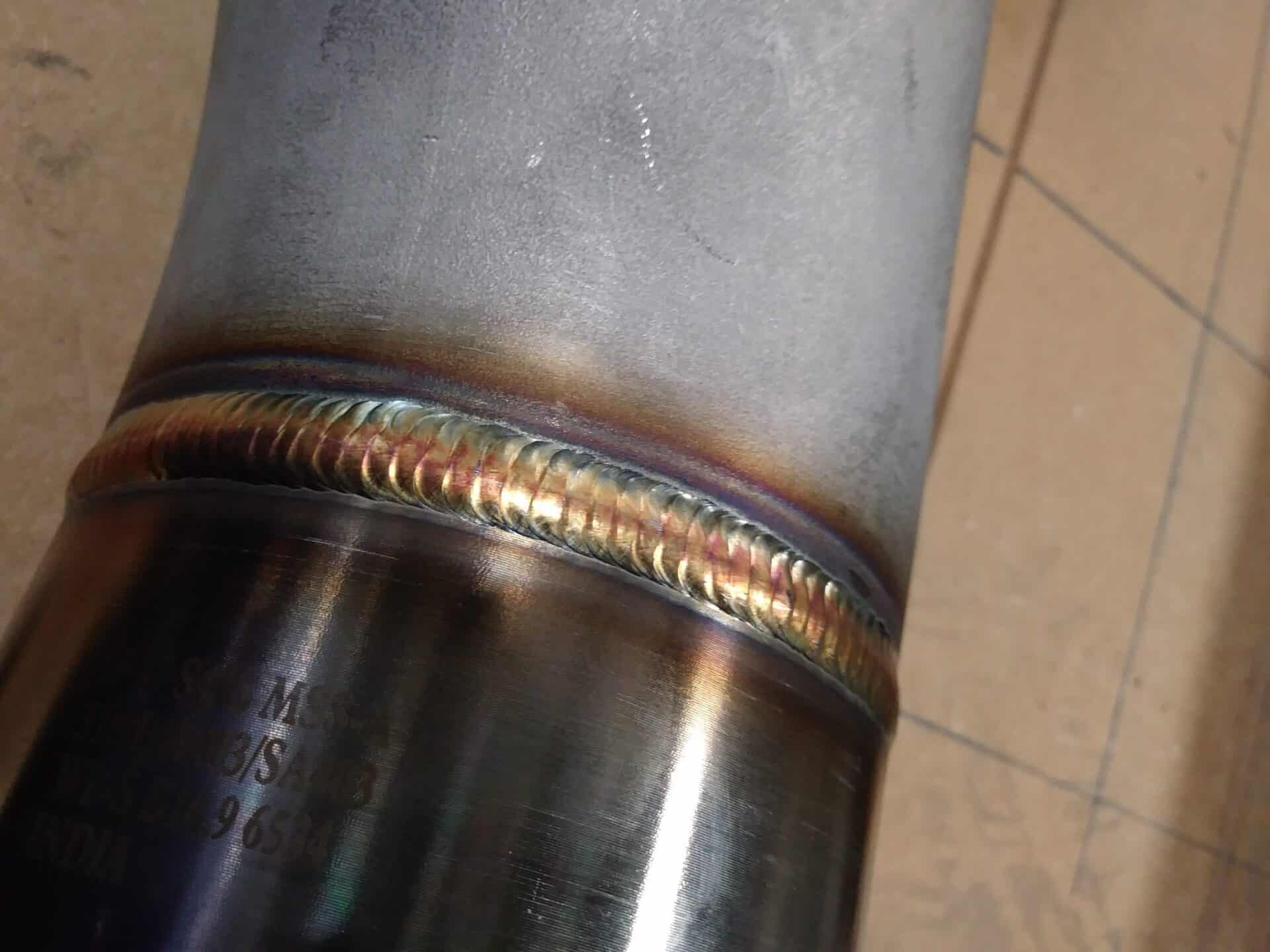